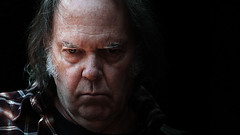
At the time Neil Young was still a major influence on my Musical tastes as well as CSNY so I decided that if I was going to learn the guitar, I might as well learn the acoustic. I thought at the time that if I could play acoustic than electric would probably be easier. So I went out and bought a mid-class (which I couldn't afford) guitar that was on sale for 50% off. That guitar turned out to be a Takamine F340. At the time I had no earthly idea of what the key components were in a guitar. But luckily for me it was built well. A dreadnaught with mahogany back and sides, a solid spruce top, ebony bridge, rosewood fretboard.
This guitar has been with me on most of my life journies. Many memories in this one. Three kids, a divorce, being thrown out a top floor window and many other cases of neglect. But over 25 years later it is still in good shape, a little worse for wear but aren't we all? You can see some of the dings in the picture, but there are probably a dozen or so major ones across the front of the guitar.
My main goal was to finish the acoustic guitar my son and I started (shown above getting a fingerboard glued on). We should be set except for setting of the bridge and actually putting a finish on the guitar. Two large and daunting tasks. So I wanted some practice before I took that on. I had loaned the Takamine to a friend for a couple of years so when I went to pick it up he also had an extremely cheap no-name acoustic that he didn't want. My plan now is to practice on the first acoustic. I would like to pop the fretboard off which is tricky on an acoustic because it is glued to the thin spruce top without much support. A crack or tear here is going to be a large problem. Then once I feel I can do that I will recondition the Takamine. I would like to do a fretboard inlay (of course) and refinish the guitar in a French Polish. If I can do that successfully than I think I am ready to take on the acoustic we were building.
After doing inventory, everything still looks good. Like I mentioned before, there are several large dings and scratches across the face of the guitar. I think most if not all of them I can get out by sanding, but one or two are fairly deep and it will be interesting to see how they turn out.
Here you can see a number of marks from the closing of the case. This is funny because I bought a case to protect it and kept it in the case whenever I wasn't using it. I couldn't afford a good case however and got a cardboard one which warped and didn't close properly after...
The neck looks in good condition. A couple nicks on the back of the neck here too. Frets are worn, fingerboard is in fairly good shape with normal wear and tear. I will be replacing all that anyway. But all in all the neck looks fairly straight. I did have some string buzz at some point which I think was due to some fret wear and slight warpage of the neck. I wasn't knowledgeable enough about guitars then to think about adjusting the truss rod so I ended up putting a shim under the nut to raise the action a little which worked. Since I am redoing the neck anyway, I will probably replace the tuner, nut and bridge so I am hoping that will fix any bridge issues.
The rest of the body is good, a couple of wear points that went through the finish but no real damage. With a good sanding and finish it should look great. Mahogany is a good wood but does need special treatment to receive a good finish. Once I sand I will need to pore fill etc... Getting the lacquer off will be a challenge though. This guitar will have to endure a lot of sanding. So first things first, I will probably take the no-name guitar and pop the fingerboard, if that goes well I will plan on a new fretboard.
This is the pattern I would LIKE to use. It comes with a matching headstock and rosette. I am a little intimidated though :-). In talking with Andy DePaul he did say this is one of his more intricate and difficult pieces, however I have done about a half dozen or more fingerboards, so... will need to think this one out a little...
